Blog
The Vocabulary of Bass
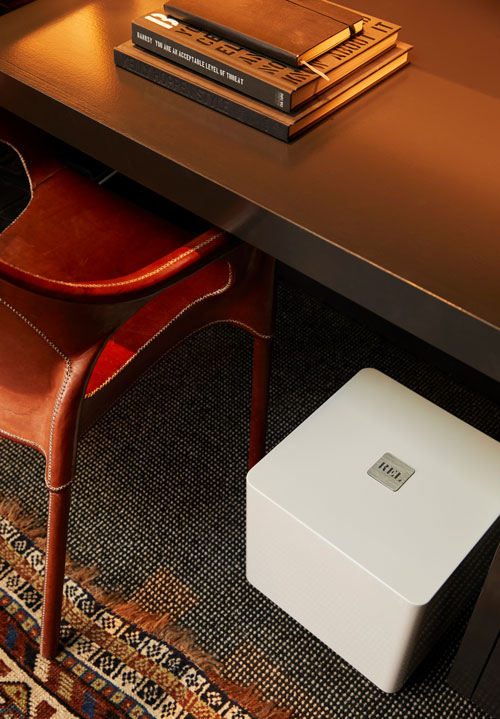
When one first begins to look into the possibility of subwoofer ownership, the uninitiated are confronted with a lot of terms to describe either physical characteristics of construction or musically relevant mathematic terms that can seem intimidating.
Measurements
Let’s start with musical and measurement terms (and the math that defines them) and work our way backward. It’s worked for me for the past 45 years. Yes, there’s a little math, but honestly, you knew how to perform most of this by the time you were out of third grade.
Our article “Measuring Up to the Competition” goes over why we conservatively measure the specs of our products and focus on long term reliability.
Octave & Hertz (Hz):
Octave (defined in Hertz, or Hz):
Such an impressive sounding term, but so very simple in its premise. An octave (if we are ascending in frequency) describes a numerical doubling. In general, the lowest octave that is quoted runs from 20Hz–40Hz. See, I promised it would be easy. The second octave would then extend from 40 Hz to 80 Hz and so on. The 10th octave is generally defined as 10,000-20,000 Hz for simplicity’s sake (but those who have done the exact math in their head will know that this rounds about 480 Hz off at the top).
If we are speaking of music descending from a higher frequency, then we are halving the same numbers. Thus, if a person owns a subwoofer that claims to extend down to 30 Hz, the octave below that would end at 15 Hz (30 x ½ = 15 Hz).
Decibel (dB):
This represents a difference in perceived loudness. A 3dB difference is a modest change in perceived output (1 dB is the smallest perceptible level of change most humans can reliably detect). 6 dB represents a significant difference and 10 dB is what we perceive as doubling (or halving) the output, by which I mean perceived loudness.
So, here’s where measurements begin and the idea, once again, is extremely simple. In order to determine how quickly a subwoofer is falling off in terms of output, we express this in terms of decibels (loudness reduction) after a certain frequency. For example, a subwoofer may have constant output to 30 Hz, then fall off in output by 6 dB below that figure. Implied in that statement is that we are speaking of falling off in output over the next octave. Those who have been patient enough to read this far will know that this represents extremely good performance as it would establish that this sub extends down quite low (32 Hz is one of the lowest pipes in a pipe organ) and is down noticeably at 15 Hz.
Extension
This term refers to how low a subwoofer extends in frequency (Hertz). When a reviewer speaks of a subwoofer having “remarkable extension”, they are communicating that the subwoofer has the ability to deliver extremely low bass. This ability correlates with the subwoofer’s ability to convey power (deep bass requires vast amounts of power) and this confers remarkable spatial qualities to the system in discussion.
Subwoofer Parts
Now let’s turn to definitions of the various parts of a subwoofer. These parts and their descriptions also cover the same parts used in normal speaker’s bass drivers (woofers) as well, the differences having to do with the robustness of construction and the resultant output possible in a quality subwoofer.
Driver:
This term defines any speaker element used to make sound in a loudspeaker, whether sub bass, bass (woofer) midrange, or high frequency (tweeter).
Frame (also known as a “basket”):
The frame is the three-dimensional round metal shape that all moving portions of the subwoofer driver are carried and supported by. In general, more expensive drivers use heavier duty cast alloy frames while less expensive ones use stamped steel frames that can still provide very good performance but do so at a price about one-third the cost of its equivalent in a die cast frame.
Magnet:
All dynamic drivers derive their electrical ability to make a cone move from the magnetic force carried within an attached magnet, generally this magnet is attached at the very rear of the frame. As a general rule, the more magnetic force (defined as Gauss) a magnet carries, the more efficient a driver becomes. However, other factors mean that a larger magnet isn’t always superior to a smaller magnet.
Cone:
This is the membrane that covers most of the visible portion of a subwoofer driver. It is tasked with producing the wavefront that delivers low bass output and impact. Various choices go into the selection of cone material with optimum choices involving reducing mass, against which must be weighed the need for great stiffness—the ability to resist bending under pressure. What pressure you ask? If the subwoofer in question is a sealed box, then the forces acting on the rear of the cone can be as high as 60 psi, while on the front (visible) portion of the cone, it sees much lower air pressure.
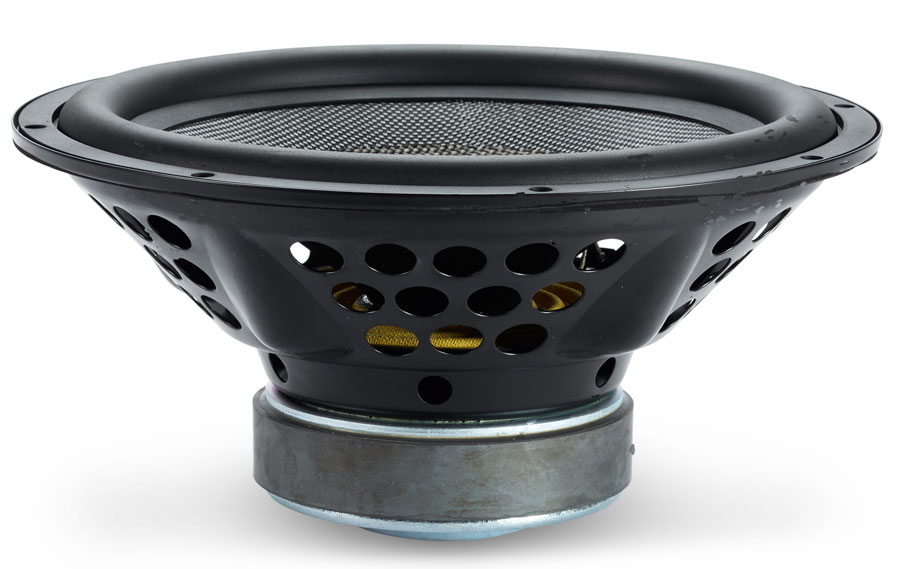
Learn what makes REL Acoustics subwoofer cones unique in our article, “Materially Superior: Not All Cones Are Created Equal”.
Surround:
A cone requires a suspension in order to allow it to move back and forth in a linear movement for millions of duty cycles in its lifespan. The surround refers to the large ring that circles the outer circumference of the cone and is used both to keep the front of the cone in perfect alignment and also to permit the extreme “throw”, or travel, of the cone backward and forward. In general, surrounds often are taller and thicker as more output is demanded from larger, more expensive designs. Recently, REL have been experimenting with the use of more complex shapes including S-shaped pleated surrounds that allow for more travel of the cone without resorting to ever taller surrounds.
Spider:
This component is one of the simpler-looking elements in a driver, but is actually very complex in both its effect on the design and the design constraints that can be imposed on the overall performance of a given driver. This item, which is almost always pleated and is made from a variety of woven fabrics, impregnated with strengthening solutions and then cooked to lock in the performance. The appearance of these vary from brownish-red to yellow to black based on the ultimate temperature needed to bake in the final performance of the spider. The spider is also responsible for delivering a restorative aspect. Simply put, if a driver is asked to move forward, there must be an inherent force seeking to move the driver back to its centered, at-rest position. Additionally, this single element is asked to maintain perfect alignment of the voice coil assembly throughout the life of the product. In REL designs, we specify very tight tolerances in our designs (typically .5mm of airgap between the copper voice coil windings and the magnet and its pole pieces) and so the precision and cost of our spiders is a significant component in our designs.
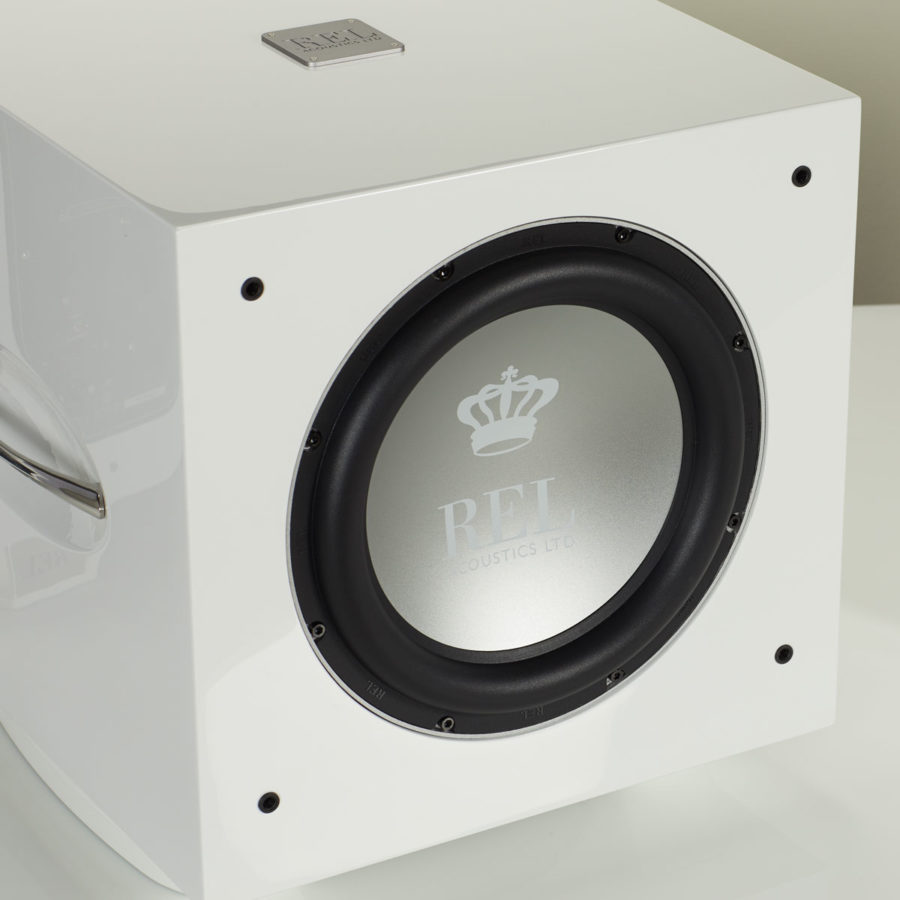
Voice Coil:
This actually refers to an assembly. The voice coil itself is assembled onto a voice coil former; a cylinder made of various materials. We generally prefer aluminium alloy to keep moving weight to a minimum and because it does an excellent job of conducting heat away from the voice coil and the specialized glues (we specify 600-degree glues that are expensive) used to keep the voice coil permanently attached. This cylinder, with a coil of litz (an extremely tough, non-conductive coating that allows the coil to act like a coil by not short circuiting) coated copper wound around, it moves back and forth in a tight air gap capped at either end by a front (North) or rear (South) pole piece. All of this is energized by the permanent magnet, which in turn is driven by the powerful amplifiers we use to deliver the electrical signal that arrives from our amplifiers and defines either music or theatre.
We hope this sequence of descriptions and definitions helps new readers and listeners better understand the mechanical process taking place within subwoofers in general, with a few tips specific to how we treat these various elements necessary in producing state of the art sub bass. What distinguishes our approach to the art of making subwoofers, is that where most manufacturers treat this more like an American pickup truck (a not entirely unreasonable approach given that the forces and demands of ultra-low bass require much beefier construction techniques), we approach the task more like a Porsche Cayenne Turbo Coupe. Still a brutally strong device, both Porsche and REL effect speed far outpacing the state of each art form; producing subtlety and fantastic dynamics via similar attention to the reduction of unnecessary moving mass and careful tuning by very experienced teams skilled at reaching to the core performance necessary for a discerning audience looking to reach farther into the performance.