Blog
Handcrafted Design
How REL Develops its World Class Cabinets
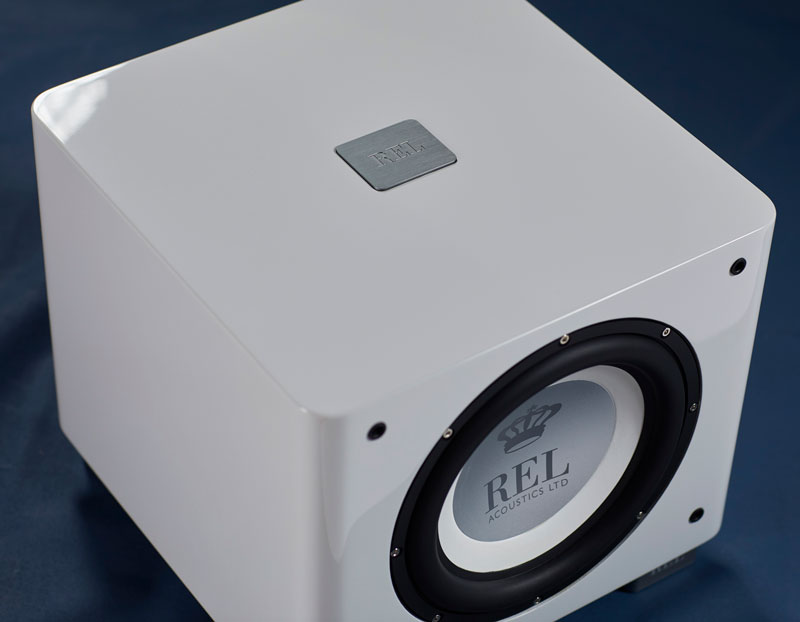
I’ve been thinking about our cabinets lately, and the more I think of it the more mysterious it becomes. Sorry, actually almost everything I do comes to me in an intuitive way based on years of experience. But I cannot always explain why it works. I just know, or can feel something should be done, in what can feel is a better way, and I act on it. And it always leads us down a path of improvement. Intuition is strange like that.
I was talking about cabinets, but it could be about why I distrust all the digital cheats that have become a way of life for most subwoofer designers. And how room correction makes no sense to me. Having worked around some of the best recording engineers in the world, I have immense respect for how critical microphone positioning is. Get it wrong by a millimeter? Two? Your results will suffer greatly. If you know enough to position a microphone like the legends you sure as hell don’t need room correction. Get it right and you have pure, unadulterated magic. It’s like that with cabinets.
One of the exercises I do when something is gnawing at me whispering “John, there’s a better way. Try this.” I stop. I stop whatever I’m doing and I sit and think, or I sleep while my inner core chews on this problem and its solution. I imagine physically what must be happening when an issue I identify comes to my awareness.
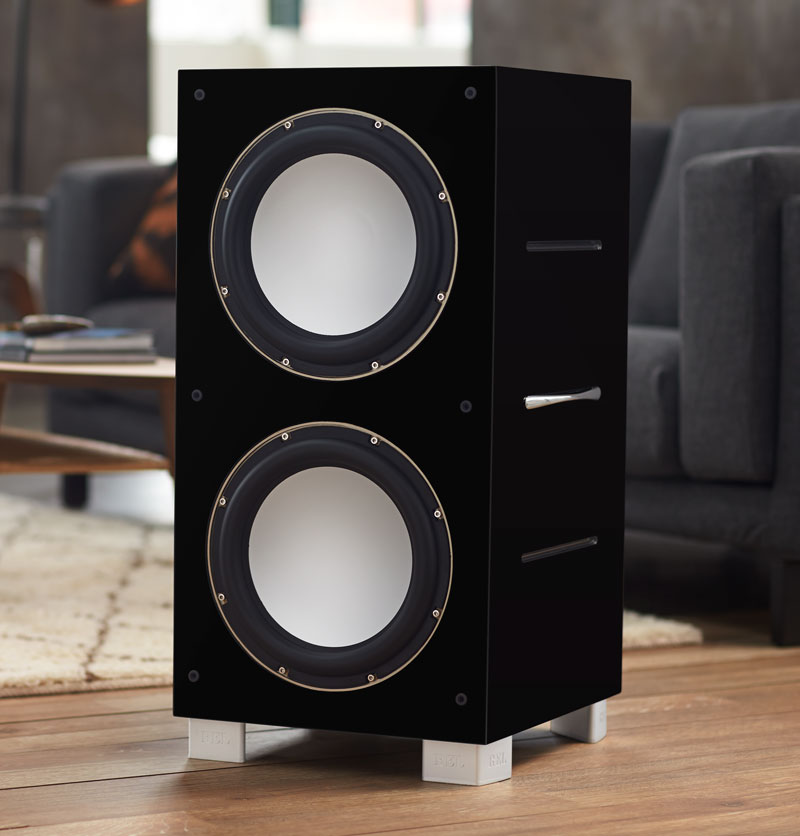
It all started with the 212/SE, a piece that was a gamble and a significant departure when we built the first ones back in 2015—it’s hard to believe now, these several years later, with 24 awards from ‘round the world. There were these weird, very rare passive radiators that would get completely and utterly destroyed that I would see pop up ––maybe 8 units in 5 years around the world. The customers all admitted, “they sometimes listened very loud”, owning up to human error being a big part of the issue. But we didn’t charge them and gave them free replacements, for which they were grateful. Still I was puzzled. I had never seen this kind of massive cone-turned-completely-inside-out damage. Imagine the opposite of what happens at a fraternity party when the party animal of the group thinks it’s funny to start crushing beer cans on his head. Think Kevin Starkie on a good night. Then turn that inside-out. What was capable of doing this? How much air pressure did it take? And why was it only ever the top rear passive radiator?
So I imagined in exquisite detail the slow motion, high pressure wavefront launching up and backward into the cabinet as the driver compressed wet, heavy air into the cavity. The pressure would shoot out in every direction, but for it not to damage the bottom passive meant that it was something to do specifically with the way the air mass in the top half of the cabinet compressed that air.
Eventually, we asked enough questions of customers that a clearer picture emerged of the stress necessary. Turned out, it was often movies, and as much as most people jump at the obvious “Oh wow, must have been a huge .1/LFE transient”, it wasn’t that. Or at least it wasn’t only that. It occurred when there was continuous, droning low frequency carrying on for significant amounts of time, building up more and more air pressure followed by a BANG! A huge transient. The heavy air mass trapped in the upper chamber would be oscillating back and forth building up more and more pressure and then when the huge transient explosion hit, the air pressure would snap the cone inside out.
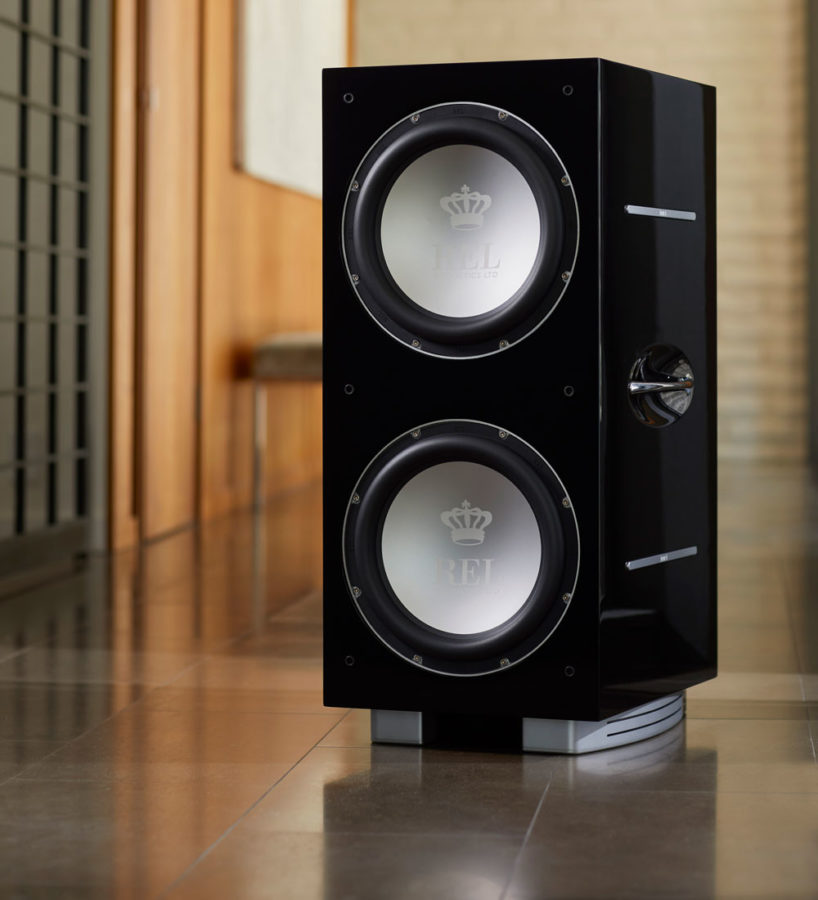
When it came time to redesign the cabinet of the new 212/SX, I “felt” my way through how I could eliminate this rare issue. Since pressure should fall off as the square of the distance between front driver and rear passive, I made the cabinet deeper. To keep cabinet volume from growing too much, I narrowed the width of the cabinet. It didn’t hurt that the new proportions instantly made the 212/SX look gorgeous and sleek, but that was more a happy byproduct than borne of a desire to make something look pretty. When combined with the new carbon fiber blades that reinforced the rear of our new active drivers, we solved our issue and made the 212/SX sound far better. Having a narrow, tighter chamber had the effect of directing the pressure wave and actually did a better job of delivering instantaneous SNAP to big bass events.
When I sat down and worked out the cabinets for the new Serie S, both 510 and 812, I used this lesson, but this time, because there was only one passive radiator and it was on the bottom, I created the squeeze of air pressure in the height, not depth of the cabinet. Again, we were rewarded with better, faster and bigger transient response. So, naturally, when we executed the new T/x cabinets I applied this lesson from the Serie S playbook and the resulting aggressively fast, dynamic signature of Serie T/x was born. More than half the sonic improvement of Serie T/i evolving into T/x is created by this cabinet rebalancing. We know this because in early testing, we auditioned most of our changes to our drivers in the old T/i cabinets. We could instantly hear the improvement provided solely by the improved cabinet proportions when we transplanted the upgraded drivers into the new T/x sample cabinets.
The point is this, so much of true progress is earned. It isn’t programmed onto tiny chips of melted sand. The stuff that truly matters? It doesn’t come from the ingenious-but-shallow results afforded by DSP or room correction. Not once have I sat down in a system “tuned” by room correction and thought “Wow, this is a hell of a system and perfectly dialed in.”
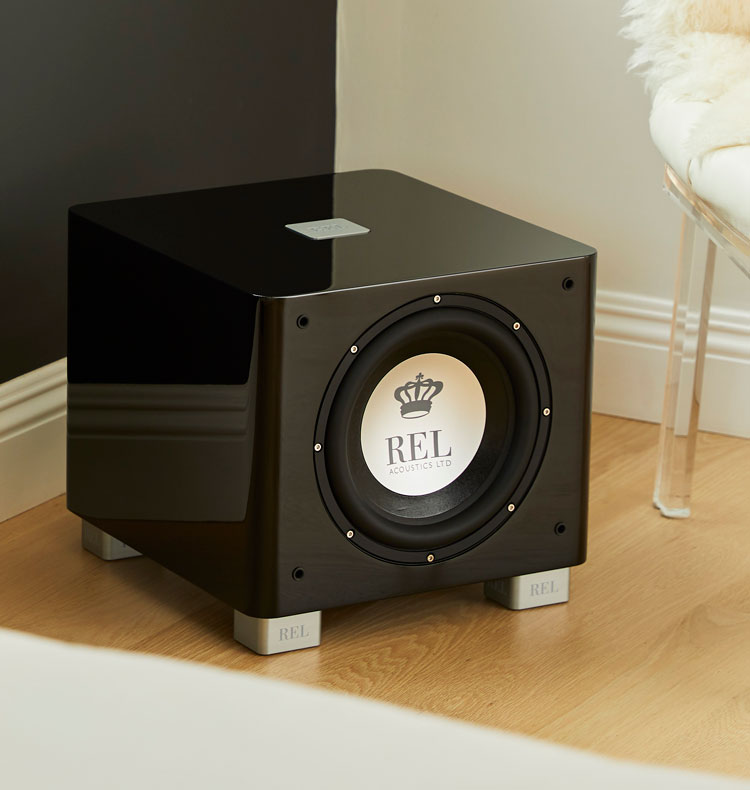
100% of the systems that stop your heart at a consumer show are carefully, patiently assembled with great care by true masters. There’s a reason we used to arrive at CES 3-4 days in advance. We left nothing to chance, took our time voicing the speakers into the room but only after running them overnight to get ourselves acquainted with the room’s idiosyncrasies. Found and quieted everything in the room that rattled. Made it perfect for our guests –the buying public– and the reviewers and dealers who serve them.
We approached it from a place of humility and service and brought the best we had to bear on the many challenges of operating under the microscope of the world’s pickiest audio reviewers in a room we had only walked into minutes before and would be our home for 48-96 hours. And we sweated all the tiny details that go into making great sound. And we NEVER resorted to the laziness of using room correction. Digital Signal Processing isn’t called Digital Really Awesome Sound Making for a reason. It isn’t. Great sound is created by men and women who work harder, longer, better. It, like everything in life worth doing, is earned.