Blog
The Making of No.31
Tomorrow Belongs to Those Who Can Hear it Coming. –David Bowie

No.31 is truly a No.32 in a smaller body.
It is that simple. No.31 delivers identical quality in every aspect of its construction. We utilize the same 1,000 watt amp, here limited to 900 watts to avoid taxing the driver beyond its incredible limits. The same dual parametric equalizers are included that are a significant tuning tool in No.32. The cabinet is constructed using the same methods (see the details on our radio frequency bombardment chambers at the end), but has been thoughtfully adapted to deliver proportional size reduction; it’s hard to tell from a short distance if you are looking at a No.32 or a No.31. This is no easy task—most who try to make a smaller version of their product mangle it. The smaller model winds up looking stubby and underfed—not so here. But there is a quiet, deeper underlying story here; one that is easily missed.
No.31 delivers the same surreal textural magic, sonic detail, definition, and air that our No.32 delivers, which has never been approximated by any other subwoofer design. Since the cabinet volume is 40% smaller, it opens up Reference-level ownership to those who are challenged by a lack of space in their primary listening rooms. It also costs 30% less while offering our highest quality.
Delivering the unique magic that No.32 and, before it, No.25 deliver in such a compact platform was tricky to design. We worked hard to develop a 12” (300mm) driver capable of handling the massive power upgrade as well as the subtlety of delivery that defines the modern REL Reference line.
Early on, we knew we needed to beef up the 12” driver. The question was, with so much less surface area to work with, how could we balance out the combination of greater power handling, and deeper stroke—No.31 measures just as loud in output as No.32—while retaining all the subtle timing cues that its larger sibling delivers? After just two months of development, we created a system that worked well. Late in the project—some two years on—we went back and adjusted several parameters to accommodate the greater power handling that our final iteration of the LimitLess™ Limiters allowed through. In other words, we found ourselves needing to return to the beginning and upgrade the very upgrade that allowed us to even approach new, higher limits.
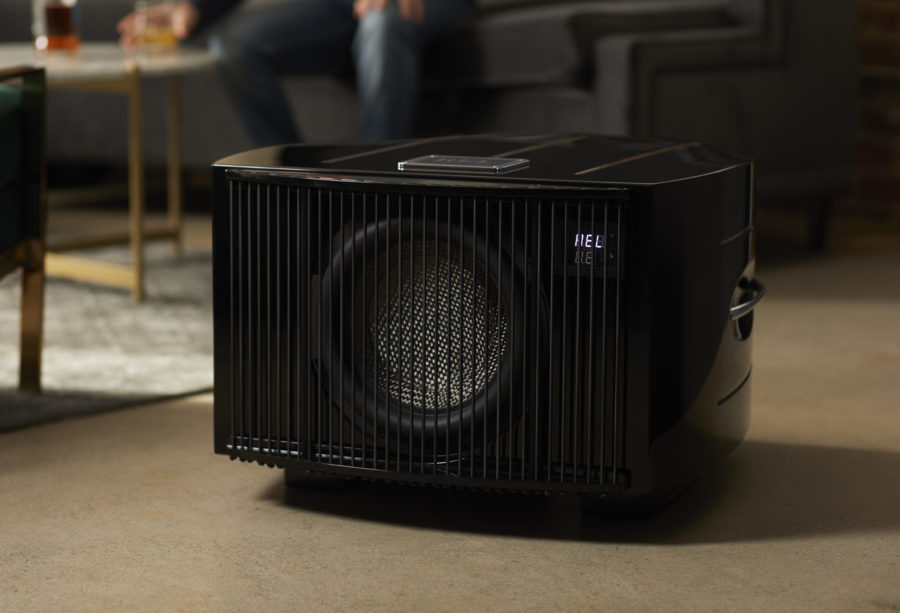
In the end, No.31’s driver is qualitatively equal to the 15” used in No.32, with identical sonic signatures. But there simply is a greater sense of ease available to a fantastic 15” driver, which even a fantastic 12” driver cannot match. However, unless you own both and run back and forth within identical systems in the same room, you’ll never hear the difference. Where the No.31 excels is the intimacy, quickness, and punch that the 12” driver delivers while extending incredibly low. It is incisive and precise yet remains warm and liquid when needed.
At just 17” in height, one of No.31’s greatest virtues is how low it lies to the floor. It is a complete 3-high line array that only comes up to the top of an average man’s diaphragm. That makes it even shorter than our own S/812 or Carbon Special models, which have allowed so many new customers to enjoy the thrills of Line Array ownership. If you’ve never heard a REL Line Array properly set up, you owe it to yourself to locate one and listen. This model opens up new vistas of performance for Reference-grade system owners who craved the transparency and dynamics of the older No.25 or the new No.32. With No.31, even decent-sized apartments and flats now have access to Reference-level sonic experiences.
We love all our designs—we’d never release a single one we didn’t feel that way about—but there is something about No.31 that has captured our hearts. It is the perfect package in both aesthetics and sonic performance. I can easily imagine building a system built around a 6-pack of these lovelies when I downsize my home. They are the fast, transparent speakers I love, but they don’t look like a tall stack of luggage about to fall on the hapless owner. This will keep my wife and me happily spinning records or CDs.
Best,
J
The construction methods used for the formation of both No.32’s and No.31’s cabinets.
That curvilinear cabinet was significant not just for its beauty, but for what it could do for sound quality… What we brought to the table was the “how” of making such a giant cabinet perfectly repeatable, which was no easy task.
Today, each No.31 is built the same way, using two large custom forms that precisely define both the positive and negative curvatures required. We load thick 30mm billets of Australian MDF into an RF (radio frequency) bombardment chamber. Then, the billet, having been placed on a perfectly flat surface, undergoes bombardment of energy until the binding agents and glues just begin to soften and release. Then, we quickly and gently slide it onto the bucks, those positive and negative curved jigs. A huge hydraulic ram presses the positively curved form into the softened billet of MDF. Then, the female curve accepts the billet until it exactly fits the lower form. These remain—locked as though in a fight to the death—overnight. The billet cools all the way back down to room temperature straight through its core.
In the morning, the process begins anew with a fresh billet in the chamber. By the second day, we have both sides necessary to begin building a single No.31. All told, the process to build the two sidewalls of one cabinet requires 21 steps, 48 hours, dozens of skilled workers, and a half-million-dollar chamber. We haven’t even gotten to the cabinet top, bottom, or inner plywood braces, which resemble giant instrumental bracing like that found in a guitar body. It takes five weeks to build a single cabinet and finish it.