Blog
REL’s Driver Focused Design
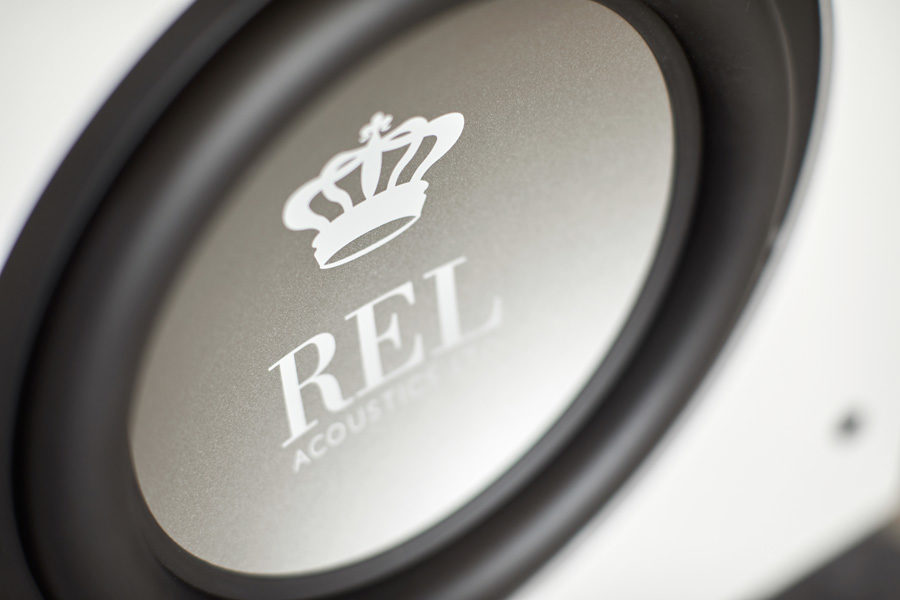
Once we define our goals for a new range, or in this case a complete upgrade of a previously successful range like Serie S, our attention turns to the drivers. The original Serie S was our first time developing the extreme throw distances necessary to create modern high output subs. At 2” fore-and-aft both our 10” and 12” drivers had plenty of throw available. But now, with the S/812 and S/510, we are throwing anywhere from 20 to 100 percent more power at the drivers, and knew that the original designs were not up to the task.
A brief examination of our toolbox was necessary, and I went through what we were working with: ultra-lightweight .5mm thick aluminium cones. Check. Oversized surround, hmm kinda check, but might need more. Then we turn to the less understood internal suspension, items like the spider, a pleated material used to locate and support the voice coil allowing it to remain centered throughout its stroke.
Understand something, I do not know how other manufacturers rate their drivers, but we rate ours to handle full power for 24 continuous hours of use. It’s an impressive feat of engineering, but ensures that rarely do REL drivers fail, short of an act of profound and prolonged stupidity.
After studying every part of the driver, visualizing what various elements must do under stress and using finite element analysis to confirm these findings, we found that we needed to subtly alter the dynamic balance of the moving structure of the driver to allow it to fully partake of the continuous levels of large motions and instantaneous dynamics we were about to require of them.
And lastly, somewhat weirdly, we had to arrive at a solution for the S/812 12” driver that would allow it to not explode under severe air pressure loads. The easiest solution to this is to make the cone thicker (more aluminium) which strengthens it, however, it also, destroys its sound quality making it sound thick, heavy, and slow –more of a conventional subwoofer, but certainly not a REL. This option was of course, totally unacceptable.
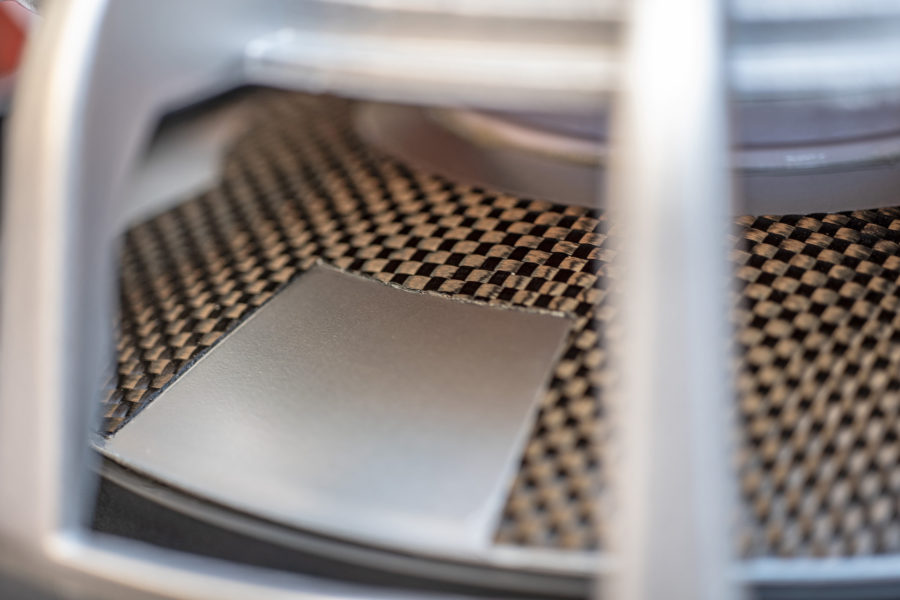
So, we revisited an idea I had developed 5 years ago during the original development of Serie S which at the time used lightweight Styrofoam backing to quiet and damp the cone (small vibrations can make a woofer lose the sense of power needed). This time, I selected carbon fibre applied over less than 50% of the rear surface of the driver. It added less weight than a single sheet of thin paper and yet stiffened the structure enormously and also paid big dividends in quieting down the driver’s surface creating a much more powerful delivery of deep bass.
Lastly, we re-wrapped the coil windings on the voice coil focusing more windings within the magnetic gap, allowing us to maintain better control of the cone throughout the total 4” of stroke the driver would “see” at full power.
When you next look at our stunning drivers with their light gunmetal grey cones and the lovely REL Crown logo proudly emblazoned, think of all the work that went into building a structurally better driver, behind all that beauty.