Blog
The Birth of G-1
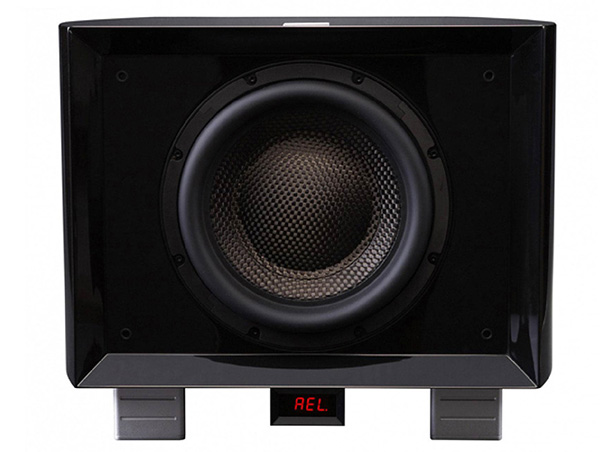
The year was 2008, and the world was gripped by the worst economic meltdown since 1929. Fear was everywhere, palpable. People rushed home to see what financial catastrophe had occurred that day, the stock market dropped—frequently—by hundreds of points a day.
In an industrial building in Berkeley, two men who worked for REL tried to block out the noise and concentrate on the sound. Bill Hermann was then a brilliant young electrical engineer, the apple doesn’t fall far from the tree. Years ago, back in the ‘80’s, his father Willy had mentored a young audio salesman who took far more than a passing interest in audio. Willy could have done almost anything, but he grew up in the ‘60’s, music was everything back then and after graduating from Johns Hopkins became the greatest audio technician on the planet—big companies like Nakamichi brought their problems to our tiny audio store and Willy solved them. Instantly. When the opportunity came, I hired Bill on the spot. His son Bill was just as smart and fast, but an engineer, not a technician.
Speed Matters
When Donald and I took over REL from Richard in 2005, we identified three things that REL and subwoofers needed to improve upon. The most important was speed, subwoofers were simply far too slow. Conventional engineers focus on flatness of frequency response and low bass extension—very important to be sure. But the difference REL has always made, is our products have always seemed to blend with, support and make music with ultra-high end music-based systems more than any other. And high-end speakers by 2010 were getting very fast. So I told Bill, “We’re going to fix this, and we don’t have a lot of time to throw at the problem. So answer me this—how fast can an active filter be—we know the crap everyone else is using are too slow. How fast is fast?”
As it happens, Bill reported back that 4 milliseconds was the technical limit of speed through a crossover. So we set about building the fastest crossover which, as it happens, isn’t all that easy. Along the way, we built several samples that were slower. We developed an 8 ms filter set which we retained because it was the first time we had experienced noteworthy performance; performance that from a high end audio perspective got us fast enough that our subs outfitted with this version of our filter sounded significantly better than anything we had previously heard. This 8 ms version is used today in everything BUT for the Reference models which use the true 4 ms filter. Bill took about a month of working hard for far longer than his 8-hour days, using various different components before he finally felt convinced that his 4 ms filter was working properly.
Pro Tip:
During that time, Bill built a digital version of the filter, but we abandoned it when it revealed itself to sound nowhere near as good as the analog version.
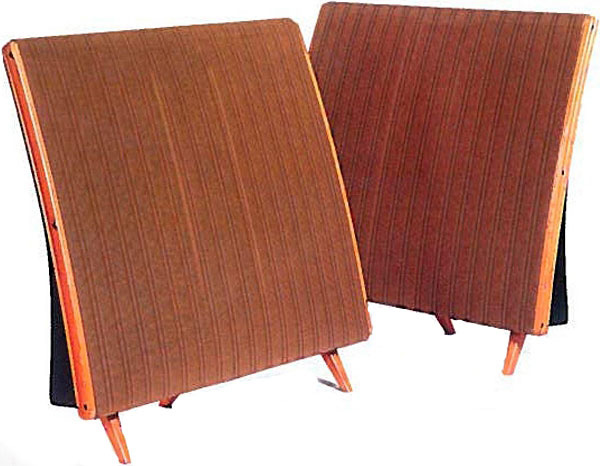
Every once in a while, you experience something in audio that you know even as you’re hearing it for the first time, this is important, this is significant. Among these moments were the first time I ever setup a moving coil cartridge and heard speed, transparency and devastating dynamics courtesy of a Denon 103C, the first time I finally coaxed a near perfect set out of my new Quad Electrostats –people began referring to them as Quad 57’s sometime in the late ‘90’s but for 30 years, they were simply “the electrostats”.
Listening to the prototype of the analogue G-1 4 ms filter was one of those moments. The instant it fired up, I was immediately aware that I was hearing through the subwoofer, not to it. The transparency was immediate and correct, and not just in the bass regions but up through the 9 octaves above. Bass was suddenly both airy and effortless, it retained proper weight and dimension but rather than announcing itself as separate and distinct was simply one with the excellent Cremona M speakers we were using.
Carbon Fibre
Meanwhile I had been hard at work designing the carbon fibre driver of my dreams. Carbon fibre having long established itself in my experience as the only technical material capable of sounding natural, in the way that paper actually allows music to sound natural, but with so much greater strength and lower mass as to make it virtually a miracle material. Carbon fibre derives so much tensile strength from the fibres being twisted into multiple larger strings or ropes which makes each such element massively tough, then hundreds and thousands of these being woven into flat sheets. At each point in the process, the material is made tougher, quieter and imparts no discernible signature, unlike woven technical materials like Kevlar that has a distinctive ringing peak to the upper midrange.
What resulted was a 12” (300mm) carbon driver, miraculous for its lightweight moving mass and incredibly long stroke (4” fore-and-aft from peak to peak). At first, we struggled in production with the small lead-in wires that carried the amplified signal to the cone going open, as though there was an invisible break in the wire. Using nothing more sophisticated than a strobe light, I was able to see that the problem was simple; it was literally accelerating so fast you could see the wires momentarily stopped or frozen while the cone had shot back in the opposite direction. Literally, the wires couldn’t keep up with the cone! We solved that issue by attaching extra-long wires, then attaching tiny spots of them to the spider so that the movement was supported along the length of the wire.
Form Follows Function
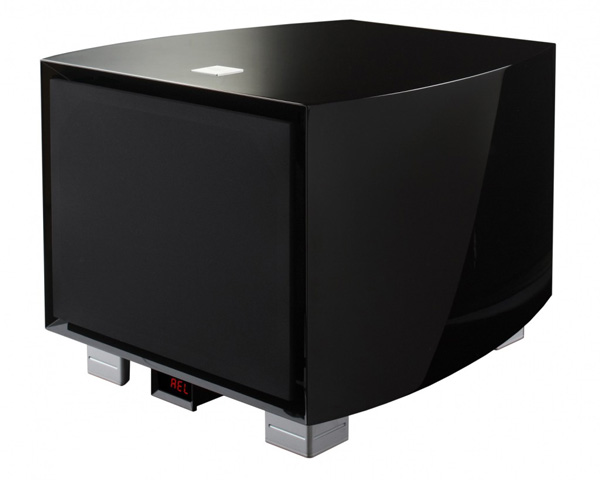
Once I had the driver solved, I worked out a design for our cabinet—we tried several shapes but the version using curvilinear sidewalls sounded clearly better in every regard. But it was very tricky to build and even minor deviations could degrade the sound noticeably. We tried to build these cabinets at our factory in Sheffield, England but several things kept us from doing so. Cost was so very much higher, the original G-1 sold in the US for $4,500 eventually rising to $5,500. Had we remained with our own factory, it would have started at $7,000 and by now sell for $10,000. They also struggled with dimensional accuracy on such a large, curved cabinet and could not deliver the glossy lacquer everyone was asking for.
Fortunately, we were by then working with the finest factory in the world for cabinet making and they asked me to fly over so they could show us how they planned to build our new design. Today, both the No.25 and G-1 MKII use this method; multiple, thick (1 1/8”, 30mm) sheets of MDF are put into a massive RF (radio frequency) bombardment chamber and hit with just enough energy to turn the binders and glues in MDF warm and soft, then they are quickly transferred to a heavy curved jig. The soft panels and huge heavy wooden form are put into a huge hydraulic press that has a matching curve. The panels are rammed into the curved form, then allowed to cool for 24 hours. When cool, the panels are perfectly formed into curves and are ultra-stable and dimensionally accurate. The result is a sexy looking cabinet that breaks up the rear-firing waves that are forced backward off the driver to create fast, deep, powerful bass without obvious box resonances. That is, after 12 hand applied coats, each sanded by hand, are applied to the cabinet and three different stages of polishing by machine and hand leave that thick, perfect gloss that looks as though you could put your hand into a still, dark pool of liquid black paint.
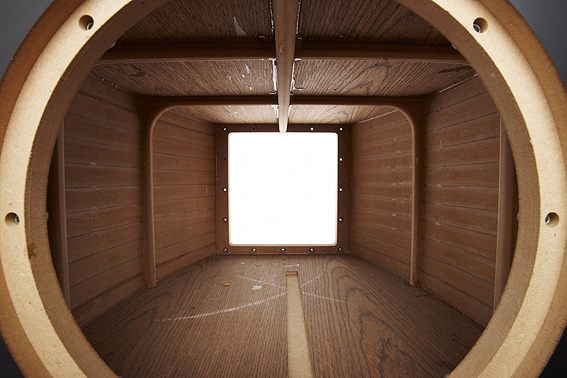
It’s been fun to share some of the challenges the original team faced. But more importantly, this exercise pushed REL to the very technical limits of what we—hell—anyone had ever tried to accomplish with subwoofer design before. There are several important products that REL have developed. Important because they went on to inform everything we have done since, the original Studio of the mid-90’s was one such. Such a design was the original 2010 Gibraltar—also known as the G-1. This breakthrough design has begotten every modern REL introduced since. Everyone who has purchased a REL since owes a debt of gratitude to this model as it created the path to the fast, coherent sound that has become REL’s trademark sound.